The commissioning and adjustment of air handling units can take a long time, and very often the units are not always installed as initially planned, leading to inefficient operation, as well as becoming a real headache for the technician in charge of commissioning.
Another frustration can be that the parameters necessary to start up the unit are not always available, meaning the system could then not function as expected, and it becomes difficult to optimise it to meet the needs of end users as closely as possible.
And when the instructions for getting an AHU started are available, they are usually done by hand, so are subject to human error!
Finally, the use of a building is very often changes. Therefore, this often involves making adjustments to the ventilation system. To do this quickly and efficiently, we need to know exactly how the air handling unit is configured. This can prove to be a challenge if the initial commissioning protocols are not available, if they're incorrect, or if the units documentation is not accessible.
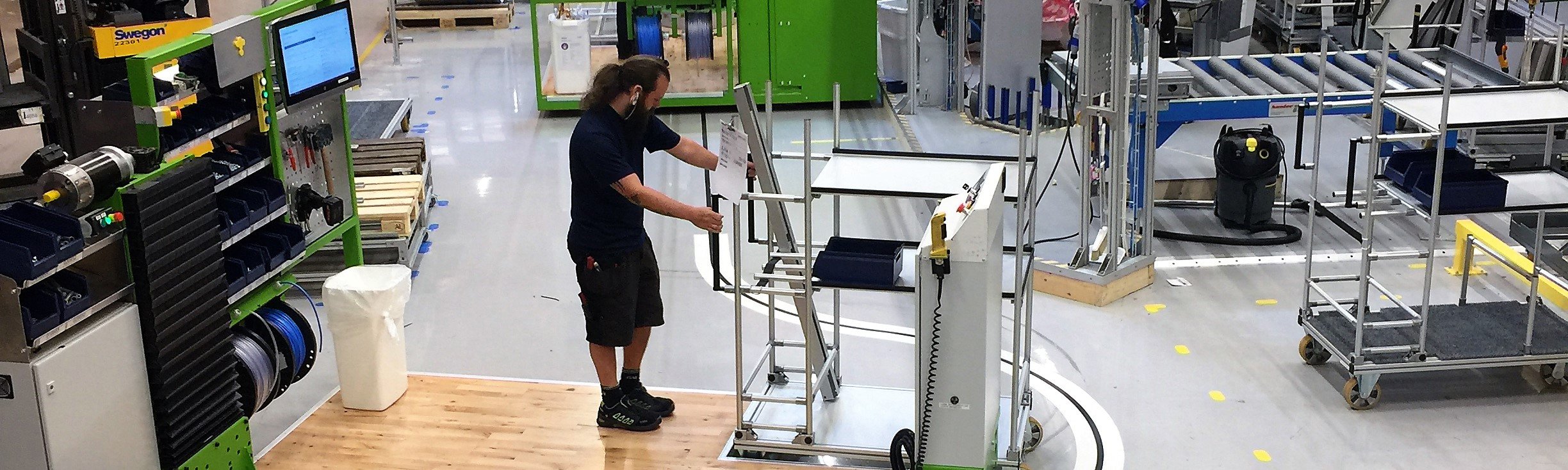
Factory configuration of control units allows for quick and easy installation.
But if we take GOLD units as an example, it is recognised that commissioning is a 'rolling business' as the preconfiguration carried out by the factory can significantly speed up commissioning time. All the information is just a click away: the commissioning report is saved in the control unit, as are the documentation relating to use and maintenance. The complete configuration of the unit can be exported to an SD card to reassure our customers and ensure quality of service. In addition, there is a fault finding aid according to the type of alarm which is intuitive for the manager and the end user. Finally, the connection of the unit to any building management system is facilitated because the communication protocols are standardised.
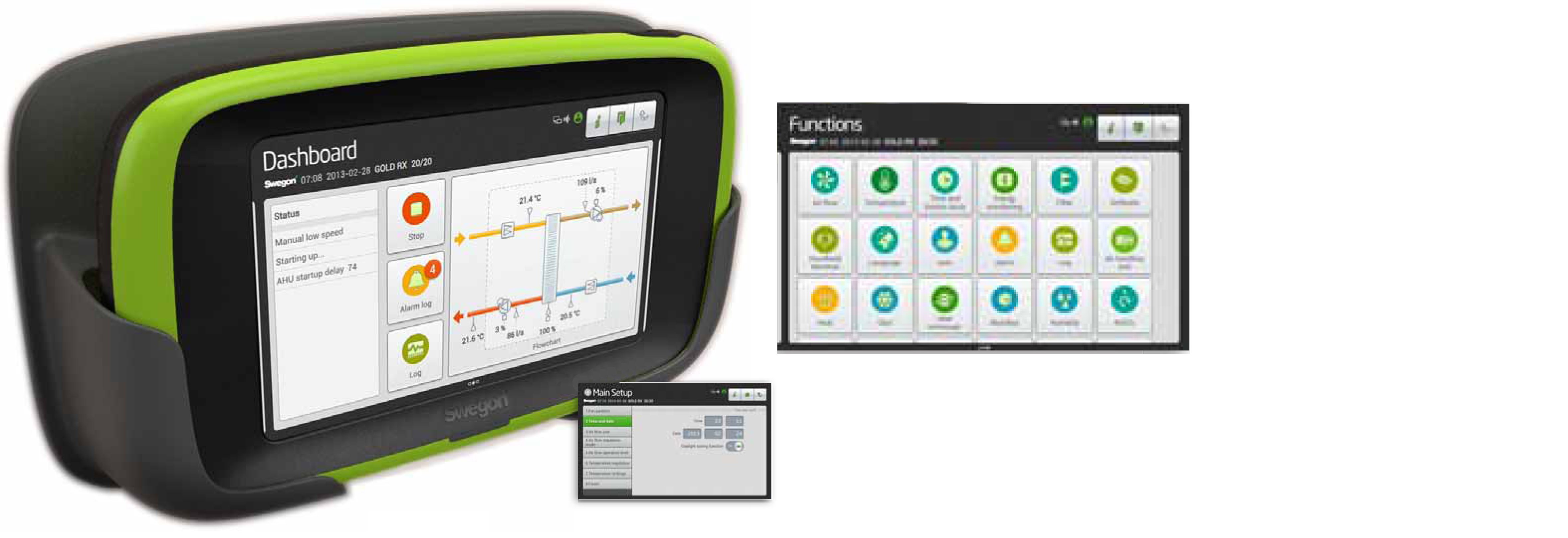
With the AHU Design selection software, it is also possible to go further than a simple selection of units and their accessories. In fact, it is possible to pre-configure the units according to the needs and requirements of each project. AHU Design then generates the documentation specific to the chosen configuration. BIM data can be customized to the exact parameters of each plant, available for MagiCad, REVIT and AutoCad.
In fact, the commissioning of the unit is partly automated as the process has been seriously streamlined which ensures that the unit operates exactly as intended and provides an energy efficient indoor climate. And the equipment is properly documented for any future updates.
What does the future of our profession look like?
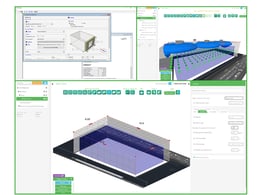
Ventilation units with factory-installed controls and BIM bring us closer to the ideal configuration of a building. By linking BIM data to plant controls, it is possible to create more value in the future. We will see that the unit can send BIM data to the building model live: it will be updated as adjustments are made. Thus the digital building will reflect the real building down to the smallest adjustment.
The fact of being in front of the unit or of accessing it remotely will no longer have any importance for a technician: the interest is to be able to commission and adjust the unit exactly when required ... but by working remotely , we will save time in terms of travel and access, and therefore we will reduce maintenance costs for customers.
Due to the fact that our equipment evolves, our profession necessarily evolves with it, it being more focused on support in the initial phases of relatively complex and very technical projects. But we must keep our two priorities in mind: time management and the economic aspect for our clients.